Deformace v důsledku svařování představují významný problém při výrobě zemědělských strojů, často vedoucí k překročení tolerancí konstrukce svařovaných sestav. Takový výrobní proces vyžaduje opakované úpravy, dlouhé zkušební časy, vysoké náklady a je závislý na zkušenostech kvalifikovaných odborníků. Pro redukci deformací během svařování a zajištění rozměrové integrity svařovaných komponent se tak běžně používají metoda konečných prvků (FEM) a CAE simulace. Ty hrají klíčovou roli při predikci deformací svařovaných sestav ve virtuálním prostředí. Například modelování a simulace deformací v hlavních rámech podvozků zemědělských strojů pomocí software Simufact Welding umožňují detailní pochopení chování materiálu během svařovacího procesu.
Výsledky validace ukazují, že numerické simulace svařovacího procesu jsou klíčové pro porozumění účinků svařování a umožňují navrhnout přípravky pro výrobu sestav v souladu s konstrukčními tolerancemi. GMAW (Gas Metal Arc Welding), známé také jako obloukové svařování plynem, je proces, při kterém se mezi elektrodou a obrobkem vytváří elektrický oblouk. Tento oblouk zahřívá materiál na bod tání, čímž dochází k jeho roztavení a spojení. Termomechanické vlastnosti materiálů jsou klíčové pro kvalitu svaru při metodě GMAW. Je zásadní je pečlivě zvážit, aby nedocházelo k nežádoucím tepelným deformacím a zbytkovým napětím, které mohou negativně ovlivnit rozměrovou a konstrukční integritu součásti.
Proces zahrnuje fázovou transformaci, která mění mikrostrukturu materiálu, což má významný dopadna jeho mechanické vlastnosti při pokojové teplotě. Tepelné deformace jsou silně závislé na okrajových podmínkách, pořadí svařování a parametrech, jako je příkon energie. Pochopení termomechanického chování materiálů a schopnost předpovědět deformace v různých svařovacích podmínkách jsou klíčové pro optimalizaci výrobního procesu.
Nastavení svařovacího procesu je často závislé na zkušenostech obsluhy a časově náročném postupu metodou pokusů a omylů, což je neefektivní a nákladné. Řešení představuje metoda konečných prvků (FEM) zaměřená na svařovací proces, která umožňuje detailní analýzu termomechanického chování svařovaných dílů a predikci tepelných deformací. Simulace svařování také poskytují cenné poznatky pro optimalizaci návrhu svařovacího procesu za různých podmínek.
Simulace svařování představuje komplexní problém vzhledem ke složitému termomechanickému chování svařovaných dílů. Jde o vícefázový a vysoce nelineární proces, který zahrnuje fázovou transformaci a plastickou deformaci svařovaných komponent.
Vývoj
Samonosná konstrukce podvozku zemědělského stroje je tvořena hlavními bočními podélníky spojenými příčníky (Obrázek 1). Toto spojení se provádí svařováním. Podvozek je konstrukční prvek, který absorbuje největší množství dynamické energie při zemědělských operacích.
Vzhledem k velkému tepelnému zatížení při svařování se společnosti rozhodly svařovat podvozek celý "zamčený", se všemi příčníky přemostěnými, aby se minimalizovaly účinky deformací.
Svařování celého rámu jako jedné sestavy může být vynikající strategií pro zvýšení produktivity a zkrácení doby cyklu. Velká výzva však spočívá v předvídání účinků deformací při svařování a nalezení řešení, které splní konstrukční tolerance.
Numerický model
Numerický model (obrázek 3) hlavního rámu konstrukce použitý v této studii je sestaven z hexagonálních Solid prvků (HEX8, v programu Simufact Welding). Pro přípravu modelu konečných prvků byl využit software MSC Apex, který automaticky přiřazoval různé velikosti prvků v oblastech s vyšším tepelným příkonem (ve sledovaných oblastech), kde byla velikost prvků nastavena na 4 mm, zatímco v ostatních oblastech byla nastavena na 10 mm. Celkový model obsahoval 389 721 uzlů a 244 557 prvků.
Materiál použitý na hlavním nosníku podvozku je konstrukční ocel s následujícími charakteristikami:
-
Modul pružnosti: 210 GPa
-
Poissonova konstanta: 0,3
-
Hustota: : γ = 7850 kg/m3
-
Mez kluzu: σesc = 700 MPa
-
Modul tangens: ETan = 431 MPa
Jako přídavný materiál byl použit ER70-S6, který má následující vlastnosti:
-
Průměr drátu: 1,2 mm
-
Tažnost: 26 %
-
Mez kluzu: 424 MPa
-
Pevnost v tahu: 518 MPa
Snížení deformací při svařování
Spojování součástí svařováním často vyvolává nežádoucí účinky, přičemž deformace patří mezi ty nejvíce kritické.
Deformace vznikající v důsledku vysokého tepelného příkonu potřebného pro dosažení tavící teploty materiálu. Tyto deformace generují vysoká napětí až za mezí kluzu, čímž dochází k pokroucení konstrukce.
Znalost metod minimalizace těchto deformací je klíčová pro efektivní řízení výrobních procesů a zajištění požadované kvality výsledných dílů.
Následující opatření jsou klíčová pro minimalizaci deformací při svařování:
-
Kompenzace: Zahrnuje vytvoření svařovacího přípravku, tak aby po dokončení procesu byla součást v tolerancích.
-
Předdeformace: Spočívá v předepnutí celé sestavy silou proti směru očekávané deformace.
-
Sekvence a směr svařování: Úprava pořadí a směrů svařování, což ovlivňuje velikostdeformací.
-
Parametry: Modifikace parametrů svařování jako napětí, proud, rychlost svařování, což ovlivňuje přenos energie a následné deformace.
-
Vlastní tíha svařence: Správné položení těžkých sestav může zmírnit deformace.
-
Svařování kritických položek na konci procesu: Aby se zabránilo deformacím spojenýms ostatními částmi.
-
Priorita pro svařování větších dílů svarů: Umožní jejich lepší chlazení uvnitř svařovacího zařízení.
-
Geometrie: Koncentrátory napětí závislé na geometrii součásti mohou vést k deformacím.
-
Okrajové podmínky: Poloha, množství a síla svorek, stolů, klínů, kolíků a dorazů mají významný vliv na deformace.
-
Chlazení: Čas chlazení uvnitř i vně přípravku ovlivňuje deformace.
Pro každou svařovanou sestavu je potřeba provést analýzu a nalézt vhodné řešení, které zajistí dodržení požadovaných tolerancí.
Numerická simulace deformací při svařování
Model konečných prvků byl připraven, se zjednodušeními a s využitím znalostí typu a formulace použitých prvků. Byly definovány velikost a množství prvků a zkontrolována jejich kvalita. Síť byla následně importována do softwaru Simufact Welding. Pro svařování byly použity parametry 295 A a 25 V pro silnou desku a 260 A a 23 V pro slabou desku. Rychlost svařování se pohybovala mezi 35 a 70 cm/min. Na obrázku 4 jsou znázorněny svary použité v modelu a na obrázku 5 je zobrazeno pořadí a směry svařování.
S přesně definovanými vstupními daty, parametry, omezeními, materiály, vstupními teplotami a trajektoriemi svařování vypočítává Simufact Welding teploty, napětí, deformace a síly v součástech pro každý uzel numerického modelu během celého cyklu. Tato data umožňují detailní pochopení chování sestavy a nalezení optimálního způsobu zajištění jejích rozměrů. Pro maximální využití této technologie byla definována metodika výpočtu. Hledání řešení bude probíhat prostřednictvím následujících kroků:
-
Analýza trendu deformací: Analýza modelu ve svařovacím přípravku k pochopení vlivu samotného svařovacího procesu na deformaci svařence.
-
Vytvoření nových okrajových podmínek: Na základě výsledků analýzy trendu deformací bude vytvořen nový model s opatřeními ke zmírnění deformací.
-
Opětovná analýza k minimalizaci deformací: Nová analýza s aktualizovanými okrajovými podmínkami pro numerické ověření úspěšnosti navrženého řešení.
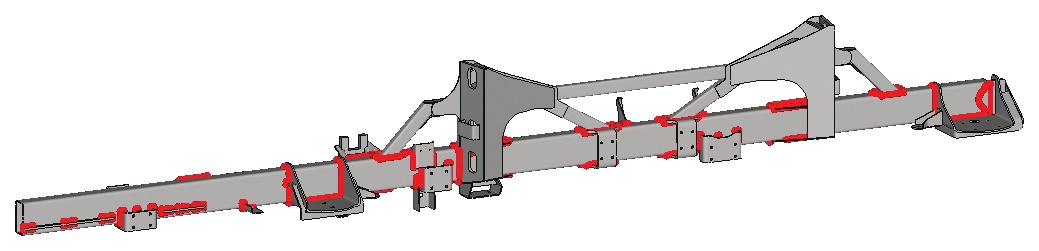
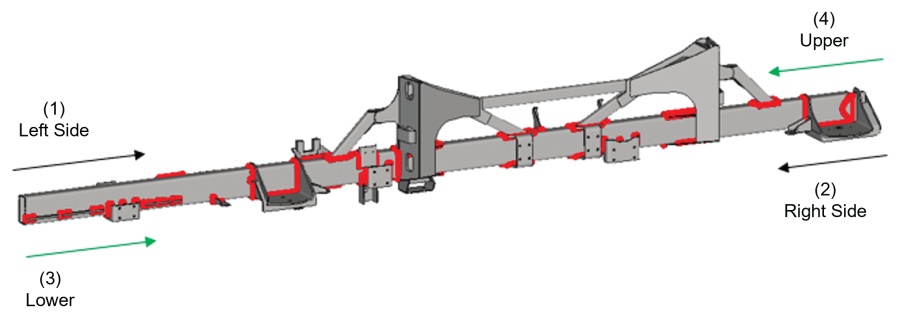
Deformační analýza
Při analýze trendu deformací byl model co nejméně omezen, pouze podepřený o stůl a zajištěný horními svorkami, aby se zabránilo jeho překlopení. Obrázek 6 zobrazuje numerický model.
Při testování modelu při pokojové teplotě (20 °C) a bez horních svorek jsme zkoumali deformace v ose „y", která je příčná k hlavnímu nosníku a kde dochází k největším posunům.
Obrázek 7 ukazuje maximální posuny modelu v ose „y". Na pravém konci hlavního nosníku byly pozorovány posuny -5 mm, zatímco ve střední oblasti došlo k posunům +7 mm. Obrázek 8 znázorňuje směr deformací ve zvětšeném měřítku pro lepší vizualizaci účinků vyvolaných svařovacím procesem.
Vytvoření nových okrajových podmínek
Na základě výsledků analýzy trendu deformací bylo rozhodnuto aplikovat na model předdeformaci. S modelem fixovaným v konstrukční poloze byly oblasti s největší deformací předdeformovány do opačného směru pomocí fixačních čepů. Na pravé straně byla použita kladná deformace 5 mm a ve středové oblasti záporná deformace 7 mm.
Model byl předdeformován v rámci elastického odpružení. Obrázek 9 ukazuje nový numerický model s předdeformací. Obrázek 10 zobrazuje deformovaný model na začátku procesu.
Opětovná analýza za účelem minimalizace deformací
Předdeformovaný model byl znovu analyzován s použitím stejných parametrů a pořadí svarů. Obrázek 11 ukazuje posuvy modelu na začátku procesu.
Po ochlazení modelu a odstranění předdeformačních upínacích sil byly analyzovány výsledky nových deformací.
Obrázek 12 zobrazuje deformace předdeformovaného modelu na konci svařovacího procesu.
Na pravém konci svařence byly maximální posuny +1 mm, což představuje snížení deformací v této oblasti o 80 %. Ve střední oblasti bylo dosaženo maximálního posunu -0,88 mm, což znamená snížení deformací o 87,4 %.
Analýza s předdeformací se ukázala jako úspěšná při minimalizaci deformací během svařování.
Konstrukce svařovacích přípravků
Výsledky získané při svařování pomocí softwaru Simufact byly zásadní pro návrh svařovacího přípravku. Koncepce přípravku byla přímo odvozena z analyzovaných modelů. Simulace umožnila určit sílu potřebnou pro předdeformování svařované konstrukce, což usnadnilo a optimalizovalo výběr hydropneumatických válců.
Obrázek 13 ukazuje analyzovaný model s řešením pro minimalizaci deformací. Na Obrázku 14 je znázorněn návrh svařovacího přípravku a obrázek 15 zobrazuje robotickou buňku pro svařování hlavních podélníků podvozku zemědělského stroje.
Simufact Welding měl pro tento projekt zásadní význam.
S pomocí této technologie bylo předem zjištěno celé chování hlavního podélníku před fyzickým svařováním. Byl optimalizován svařovací přípravek, pauzy pro ochlazení a síly ve válcích svařovacích upínek. Tímto došlo k výraznému zkrácení zkoušení a testování.
Hlavní podélník byl svařen a poté naskenován zařízením Absolute Tracker AT960 s laserovým skenerem AS1, sondou T-Probe a pomocí softwaru PC-DMIS byly ověřeny odchylky posunutí způsobené procesem „Digital Twin" vyplývající ze simulace „Digitálního dvojčete". Obrázek 16 ukazuje proces měření/skenování odchylek (v mm) pro pro pozdější vyhodnocení a porovnání výskedků simulace modelu digitálního dvojčete a reálného svařence podélníku.
Obrázek 17 ukazuje odchylky (v mm) pro svařovaný podélník, které se nacházejí v tolerancích požadovaných výrobním týmem.
Simulační software Simufact Welding |
Simufact Welding je nástroj pro modelování a optimalizaci tepelných svařovacích procesů, který bere v úvahu postup svařování a použití přípravků. Tepelné deformace a zbytková napětí po neoptimalizovaném svařování a upnutí představují při svařování zásadní problém. Tyto vlivy často způsobují, že výsledná sestava nesplňuje geometrické tolerance, což komplikuje následnou montáž. S využitím technologie Simufact Welding je možné svařovací proces i jeho parametry optimalizovat tak, aby byla zajištěna požadovaná kvalita výrobku. Simufact Welding podporuje návrh a optimalizaci svařovacího procesu prostřednictvím:
Software je navržen s ohledem na uživatelskou přívětivost a intuitivní ovládání. |
Obchodní oddělení Praha
Jana Tvarohová
E-mail: jana.tvarohova@hexagon.com
Mobil: +420 727 983 625